Quality standards in construction are inferred metrics based on quality control. Hence, to fully understand the concept of quality standards, there’s a need to define quality control. Construction quality control refers to the systematic management of processes and practices that ensure the end product meets or exceeds the standards and guidelines set by the client and regulatory authorities. It involves a combination of quality assurance (setting expectations) and quality control (implementing plans and procedures to achieve those expectations).
Importance of Quality standards in construction projects
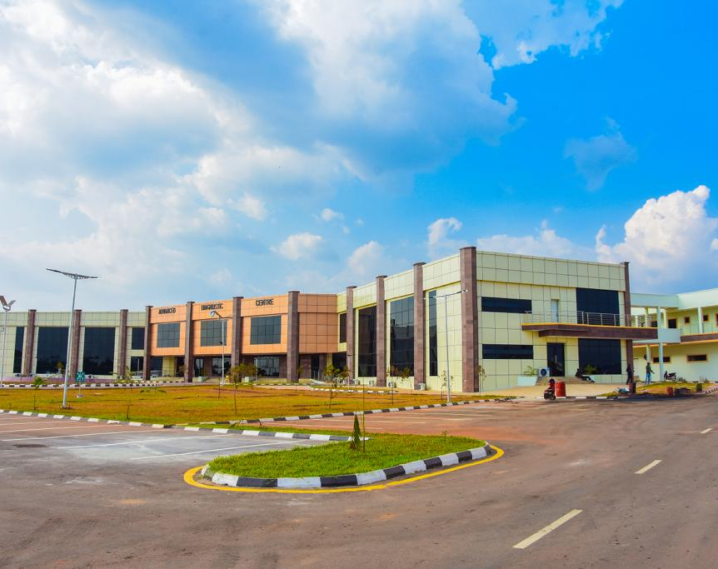
Top construction companies worldwide place a high emphasis on the standards of their projects. They do this by employing the best in their fields and providing the materials with the best quality to ensure a quality job is done. They know, by data and experience, that quality. Data has shown that quality standards also affect the ability of construction companies to get funding and their reputation in the market.
Construction companies build their organizational models to ensure that at every point in the project, the quality standards of materials used are high and right to use. Poor quality work has a detrimental effect on the company. For instance, using low-quality materials and construction practices could lead to injuries, accidents, and fatalities during and after construction. Other detrimental effects include financial implications of poor quality standards, delays and errors in construction, etc.
When construction companies implement effective quality control procedures, they can improve project efficiency and productivity. By consistently meeting or exceeding quality standards, construction teams build trust with clients and stakeholders, increasing confidence in the company’s capabilities and reliability. This, in turn, can open up new business opportunities and foster long-term partnerships.
How to ensure quality standards in construction projects
The importance of quality standards in construction projects can not be overemphasized. It spans every stage of construction. However, knowing the importance is not enough; there’s a need to have step-by-step instructions to ensure these standards are upheld at all levels of construction. Here are steps on how to ensure quality standards in construction projects:
Clearly define the acceptance criteria for quality standards:
This involves detailed discussions with the client at the beginning of the project to understand their specific requirements and preferences. It’s essential to document all the agreed-upon criteria for the final product, including technical specifications, materials to be used, project deadlines, and compliance with relevant codes and regulations. Having a well-defined scope of work and quality criteria ensures that everyone involved in the project understands their roles and can effectively work towards those common goals.
Always schedule an inspection:
A well-structured inspection plan involves identifying key milestones throughout the construction process where inspections will take place. These inspections should occur at critical stages, such as after completing foundation work, pouring concrete, electrical and plumbing installations, and project handover. Each inspection should have specific criteria to check and verify that the work meets quality standards. Inspections can be performed by trained internal quality control teams or independent third-party inspectors to ensure impartiality.
Have a checklist of things to check during quality control inspection:
The checklist acts as a practical tool for ensuring consistency and thoroughness in quality control. It should include all the critical elements to be checked during inspections, specific tests to be conducted, and a list of potential issues to be addressed. The checklist can also outline responsibilities, ensuring that each team member understands their role in maintaining quality and adhering to the project requirements.
Have measures to correct deficiencies:
When issues or deficiencies are identified during inspections, they must be promptly addressed. Construction companies should have a structured process for documenting and resolving these issues. This process may involve rework, material replacements, or adjustments in construction practices. Quick and effective resolution of problems helps avoid costly delays and potential rework later in the project.
Have review sessions after each project:
It’s crucial to learn from past projects and continuously improve quality control practices. After completing a project, construction project managers should conduct post-project reviews to analyze any challenges faced during construction and the effectiveness of the quality control procedures. This feedback loop can provide valuable insights for future projects, enabling the company to continually avoid repeating the same mistakes and refine its quality control process.
By incorporating these detailed steps into quality control management protocols, construction companies can significantly enhance the likelihood of delivering successful projects with superior quality, thereby fostering client satisfaction, building a strong reputation, and ultimately thriving in the competitive construction industry.
Contemporary Group Limited
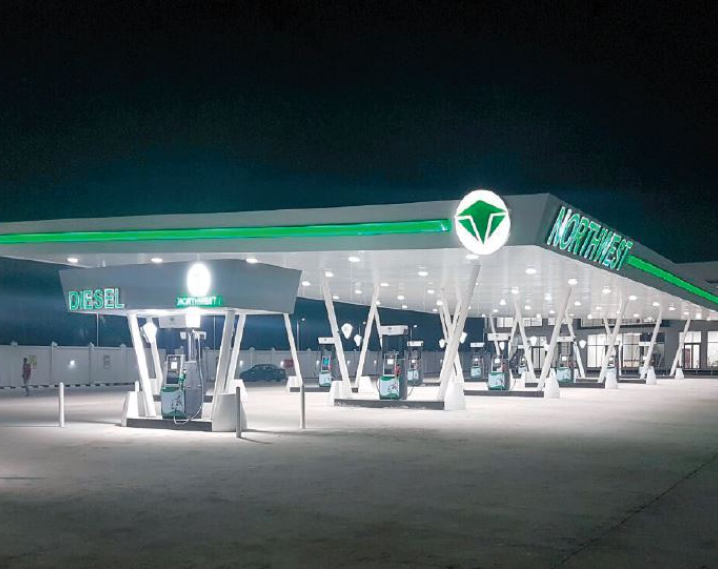
Contemporary Group Limited is a top-rated construction company that delivers your dream structures into reality. We are top professionals who dedicate experience, expertise and top quality survey to giving you the best. We are specialists in all forms of construction services. If you have been looking for that construction company that needs to birth your vision and dream, here we are. Contact us to make your dream structure come true.
standards in construction – standards in construction – standards in construction